Wet flue gas desulfurization, flue gas through the absorbent contained in the aqueous solution of the reaction, the absorbent can use ammonia or sodium sulfite and other materials. But the more widely used is the use of lime or limestone slurry as absorbent. The use of lime or limestone slurry, so that the tail of the boiler flue gas in the spray tower with the contact reaction, the slurry of calcium in the flue gas with the reaction of SO2 to generate gypsum, while removing other pollutants in the flue gas, such as dust, HF , SO3 and the like. To this end, the tower should be installed outside the large-scale circulating pump, circulating to the tower supply limestone slurry. In addition, some auxiliary pumps are also required, such as pre-wash pumps for lime slurry systems and pumps for gypsum drainage.
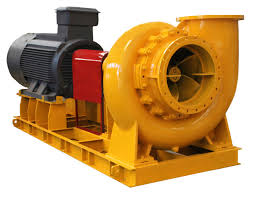
Limestone slurry contains chloride ions (20000 ~ 60000) X10-6, pH 4.5 ~ 7 between the concentration of 20% to 35%, up to 60%. Desulfurization pump over-current components must be selected with anti-wear and corrosion resistance of the material, a rubber lining, lining ceramic, all-metal alloy and other materials.
Desulfurization pump generally used cantilever single-stage single-suction centrifugal pump, the specific speed is generally 250 ~ 350. Impeller can be designed in accordance with the general method of centrifugal pump, closed impeller, open impeller and so on. Taking into account the need for a long continuous power plant running time, so the cavitation and efficiency of the pump have some requirements.
Usually with a back blade, reducing the pressure of the sealed chamber, reducing wear and tear.
Adjustable axial position can be adjusted by adjusting the bearing seat, which can adjust the increased clearance due to wear and reduce leakage gap to ensure that the pump in high-efficiency operation. Or provision of replaceable wear plates.
Shaft seal with a variety of forms, packing seal, mechanical seal, vice impeller seal. General optional cartridge mechanical seal, high precision, easy replacement and maintenance, reliability is also high.
Bearing according to the different load with different forms, light load pump shell with a pair of angular contact ball bearings + cylindrical roller bearings, heavy duty pump tapered roller bearings + cylindrical roller bearings. Lubrication with a thin oil bath lubrication.